Sliding and impact plates
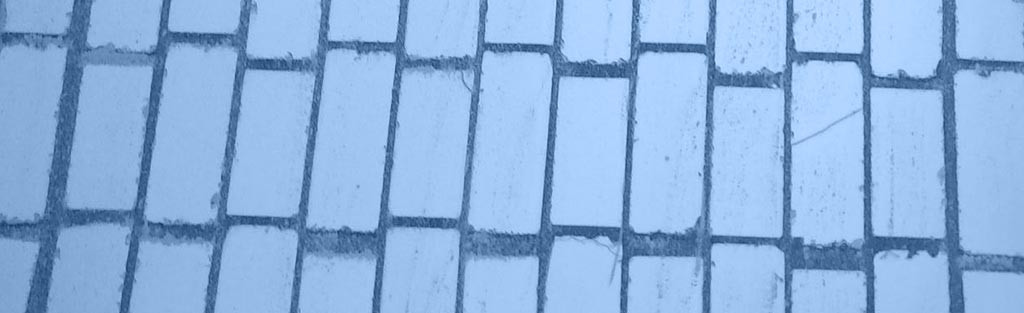
Sliding and impact plates
POLYURETHANE
Sliding and impact plates made of polyurethane are widely used in the mining industry, in the transport of bulk materials and their further processing. However, their most frequent use is for lining of slides, impacts or knots transporting material from or to conveyor belts.
Design:
- Pure polyurethane plates
- Mounting method: adhesive bonding
- Advantages: easier handling and subsequent cutting if necessary
- Disadvantages: mounting requires thorough preparation and a clean surface - Plates with embedded metal sheets
- Advantages: simple and quick mounting which does not require thorough preparation, the plates hold their shape and are suitable for more demanding applications
- Mounting methods: embedded openings (for screw fixing) available including cover plug;
threaded rod on the bottom side; magnets
Advantages:
- Very good anti-abrasive properties
- Polyurethane has a shock-absorbing capacity that can significantly reduce the noise level when the material impacts
- Easy handling and lower weight compared to conventional hard sheet lining
- Easy handling and installation
- Very good sliding properties even in contact with water
Polyurethane impact and slipping plates are recommended for light to moderately stressed applications. In case of impact of large material, we recommend some of the alternatives listed below (with the exception of wet material).
Supplied materials and dimensions:
- Supplied in dimensions according to customer requirements
- Thicknesses 5-60 mm
- Material: Polyurethane 60-90 Shore A
- Can also be supplied in antibacterial version for gravel pits
- Various thicknesses in 2000 x 1000 mm plate size in stock
RUBBER
Sliding and impact plates made of rubber are used similarly to polyurethane ones in the mining industry, in the transport of loose materials, but also in their further processing. Their most common use, however, is the lining of impacts and slides with larger material.
Advantages:
- Very good anti-abrasive properties
- The rubber is characterised by its excellent shock-absorbing capacity, which absorbs shocks and can thus significantly reduce the noise when the material impacts, but it also isolate impacts that would otherwise be transmitted to the supporting steel structure
- Easy handling and lighter weight compared to conventional hard sheet lining
- Easy handling and installation
Design:
- Rubber plate with embedded sheet metal and M16x35 bolts for attachment
Materials and dimensions supplied:
- Dimensions 200 x 300 mm
- Thickness 40 mm
- Material: 65 Shore A rubber
CERAMIC LINERS
Extreme abrasion resistance
Ceramic liners, connected with durable vulcanized rubber, are the ideal solution for high abrasive material flow. They are used in various types of chutes, impact boxes, silo liners and hoppers.
Thanks to a way of connecting ceramic elements to a steel plate by vulcanization, it is possible to utilise all the unique properties of the used elements in one product. The ceramic liners provide unrivalled abrasion resistance to abrasive materials, while the special rubber acts as a shock absorber to protect the ceramics from extreme impacts that could otherwise damage it.
The fastening of the liners on the steel plate is enabled by a simple method of anchoring, either using anchor holes or embedded screws, according to the customer's requirements.
Field of application
- quarries
- gravel pits
- steel industry
- mines
- recycling
- other industries
Types of ceramics liners
The ceramic liners are produced in 4 designs, which differ according to the material to be transported. The production of abrasion-resistant liners is custom made according to the customer's requirements.
According to the customer's requirements, chute plates can be supplied also in the version with fastening into various modular screen systems
80 x 33 x 5 mm
20 x 20 x 6 mm
- Used for lining chutes for high abrasion material flow
- Thin damping layer of rubber between the sheet and the ceramics (2 mm) excludes their use for impact surfaces.
- Used especially for: chutes, lining of bins and silos
- Total thickness is minimum 20 mm
20 x 15 mm
fí 25 x 25 mm
- Suitable for all impact surfaces and heavy-duty applications
- The higher damping layer of rubber (7 mm) allows them to be used also on impact surfaces and chutes with an impact slope of up to 60 degrees.
- Mainly used for: chutes, vibrating conveyors, impact surfaces, loading points, etc.
- Total thickness is minimum 35 mm
Methods of fixing the plates
- Using welded threaded rods in different lengths
- Using embedded threaded bushings
HARDOX 450
Sliding and impact plates made of Hardox 450 are the standard for the protection of heavily stressed areas in the mining, steel and process industries. They are characterized by their great durability as well as their self-supporting ability which allows their wide use in various applications.
Design and dimensions supplied:
- Plates
- Production according to supplied drawings
- Can be cut by laser, plasma, waterjet
- Various thicknesses up to 160 mm
Advantages:
- Good anti-abrasive properties
- Possibility of welding and further use in final products and applications
- Very good impact properties and shock absorption from impacting material